Il Diagramma di Ishikawa
I diagrammi di Ishikawa, noti anche come diagrammi causa-effetto o diagrammi a lisca di pesce, sono strumenti essenziali per identificare, analizzare e rappresentare graficamente le cause potenziali di un problema specifico. Sviluppati da Kaoru Ishikawa negli anni '60, questi diagrammi sono ampiamente utilizzati nella gestione della qualità e nella risoluzione dei problemi.

1. Cos'è un Diagramma di Ishikawa?
Un diagramma di Ishikawa è un diagramma che aiuta a visualizzare le molteplici cause di un problema (effetto).
La struttura del diagramma assomiglia a uno scheletro di pesce, con il problema rappresentato nella "testa" e le cause suddivise in categorie lungo le "lische".
Di seguito vedremo di spiegare meglio il concetto per rendere più chiaro e fruibile questo importante metodo, uno dei più completi e utilizzati per analizzare e sviscerare i problemi, di qualsiasi tipo, con i quali dobbiamo spesso confrontarci.
2. Struttura del Diagramma di Ishikawa
Il diagramma di Ishikawa ha una particolare struttura che ci aiuta a visualizzare le sfaccettature del problema in analisi:
- Testa: rappresenta il problema o l'effetto da analizzare.
- Spina dorsale: una linea orizzontale che collega la testa con le cause principali.
- Lische principali: categorie di cause principali che contribuiscono al problema.
- Lische secondarie: cause specifiche dettagliate che derivano dalle lische principali.
3. Come Creare un Diagramma di Ishikawa
3.1 Definire il Problema
Il primo passo nella creazione di un diagramma di Ishikawa è identificare e definire chiaramente il problema o l'effetto che si desidera analizzare. Questo dovrebbe essere un sintomo o un risultato osservabile che richiede un'indagine più approfondita. È importante formulare il problema in modo chiaro e conciso, in modo che sia facilmente comprensibile per tutti coloro che saranno coinvolti nell'analisi.
Esempio: Il problema potrebbe essere "Aumento dei difetti nei prodotti finiti".
3.2 Identificare le Categorie Principali
Una volta definito il problema, è necessario identificare le categorie principali di cause che potrebbero contribuire a causare l'effetto indesiderato. Le categorie comuni, conosciute come le "6M", includono Metodo, Macchina, Manodopera, Materiale, Misura e Ambiente. Tuttavia, a seconda del contesto specifico, potrebbero essere necessarie categorie aggiuntive o diverse.
Esempio: Per l'aumento dei difetti nei prodotti finiti, le categorie principali potrebbero essere Metodo, Macchina, Manodopera, Materiale e Ambiente.
3.2.1 Identificare le Categorie Principali: Le 6M
Quando si crea un diagramma di Ishikawa, è importante suddividere le possibili cause del problema in categorie chiare e significative. Un modo comune per fare ciò è utilizzare le "6M", un acronimo che rappresenta sei categorie principali di cause che possono contribuire a un problema.
Queste categorie includono:
- Metodo - Si riferisce ai processi, alle procedure o ai metodi utilizzati per svolgere un'attività. Le discrepanze o i problemi nei metodi possono portare a inefficienze o a risultati indesiderati.
- Esempio: Procedura di Controllo della Qualità - La procedura attuale per il controllo della qualità potrebbe essere inefficiente o non sufficientemente dettagliata, consentendo che difetti passino inosservati durante il processo di produzione.
- Macchina - Include tutte le attrezzature, le macchine o gli strumenti utilizzati nel processo. Problemi di manutenzione, malfunzionamenti o inefficienze delle macchine possono causare difetti nei prodotti o interruzioni della produzione.
- Esempio: Manutenzione Preventiva - La mancanza di manutenzione preventiva su una macchina chiave potrebbe portare a malfunzionamenti o guasti durante la produzione, causando ritardi o difetti nei prodotti.
- Manodopera - Riguarda il personale coinvolto nel processo, comprese le loro competenze, la formazione e l'esperienza. Errori umani, carenze di competenze o mancanza di formazione adeguata possono portare a problemi nella produzione o nella consegna del servizio.
- Esempio: Formazione del Personale - Se il personale non ha ricevuto una formazione adeguata sulle procedure di produzione o sulle tecniche di controllo della qualità, potrebbero commettere errori che influenzano la qualità dei prodotti.
- Materiale - Include tutte le materie prime, i componenti o i materiali utilizzati nel processo produttivo. La qualità, la disponibilità o la gestione inadeguata dei materiali possono influenzare la qualità del prodotto finale.
- Esempio: Fornitura di Materiali Difettosi - L'acquisto di materie prime di bassa qualità o la ricezione di materiali danneggiati potrebbe portare a difetti nei prodotti finiti, richiedendo scarti o ripetizioni del processo di produzione.
- Misura - Riguarda i metodi utilizzati per valutare la qualità o le prestazioni del processo o del prodotto. Errori o incoerenze nelle procedure di misurazione possono portare a una valutazione inaccurata della qualità o delle prestazioni.
- Esempio: Calibrazione degli Strumenti di Misura - Se gli strumenti utilizzati per il controllo della qualità non sono stati calibrati correttamente o regolarmente, le misurazioni potrebbero essere inesatte, portando a una valutazione errata della qualità dei prodotti.
- Ambiente - Si riferisce alle condizioni ambientali, sia interne che esterne, che possono influenzare il processo o il prodotto. Variabili come temperatura, umidità, pressione o inquinamento possono avere un impatto sulle prestazioni o sulla qualità.
- Esempio: Condizioni di Lavoro - Condizioni ambientali inadeguate, come un'illuminazione insufficiente o una temperatura troppo elevata, potrebbero influenzare la concentrazione e le prestazioni dei dipendenti, aumentando il rischio di errori nella produzione.
Queste sei categorie forniscono una struttura utile per esaminare e analizzare le possibili cause di un problema in modo completo e sistematico. Utilizzando le "6M" come guida, è possibile identificare le fonti potenziali di inefficienza o di difetti e sviluppare soluzioni mirate per risolvere il problema in modo efficace.
3.3.2 Esempio Pratico: Aumento dei Difetti nei Prodotti Finiti
Definizione del Problema
Problema: Aumento dei difetti nei prodotti finiti.
Identificazione delle Categorie Principali (6M)
Le categorie principali delle "6M" sono Metodo, Macchina, Manodopera, Materiale, Misura e Ambiente.
Dettagliare le Cause Specifiche per Ogni Categoria
1. Metodo
- Procedura di Controllo della Qualità Inadeguata
Le attuali procedure di controllo della qualità non riescono a identificare tutti i difetti durante la produzione.
- Processo di Assemblaggio Complesso
Il processo di assemblaggio è troppo complesso e manca di istruzioni chiare, portando a errori frequenti.
2. Macchina
- Manutenzione Preventiva Inadeguata
Le macchine non ricevono manutenzione preventiva regolare, causando malfunzionamenti durante la produzione.
- Tarature Errate delle Macchine
Le macchine non sono tarate correttamente, influenzando la precisione del prodotto finito.
3. Manodopera
- Formazione Insufficiente
Il personale non ha ricevuto una formazione adeguata sulle nuove attrezzature e procedure.
- Errori Umani
Errori commessi dagli operatori a causa di distrazione o stanchezza.
4. Materiale
- Qualità dei Materiali
Materie prime di bassa qualità o difettose vengono utilizzate nella produzione.
- Forniture Irregolari
Ritardi o irregolarità nella fornitura dei materiali causano interruzioni nel processo produttivo.
5. Misura
- Strumenti di Misurazione Mal Calibrati
Gli strumenti utilizzati per il controllo della qualità non sono calibrati correttamente, portando a misurazioni inaccurate.
- Procedure di Misurazione Incoerenti
Mancanza di procedure standardizzate per le misurazioni, portando a risultati inconsistenti.
6. Ambiente
- Condizioni Ambientali Non Controllate
Temperature e umidità variabili nel reparto di produzione che possono influenzare la qualità dei prodotti.
- Illuminazione Inadeguata
Illuminazione insufficiente che può causare errori visivi durante il processo di assemblaggio.
Diagramma di Ishikawa
Ecco l'esempio rappresentato nel diagramma di Ishikawa:
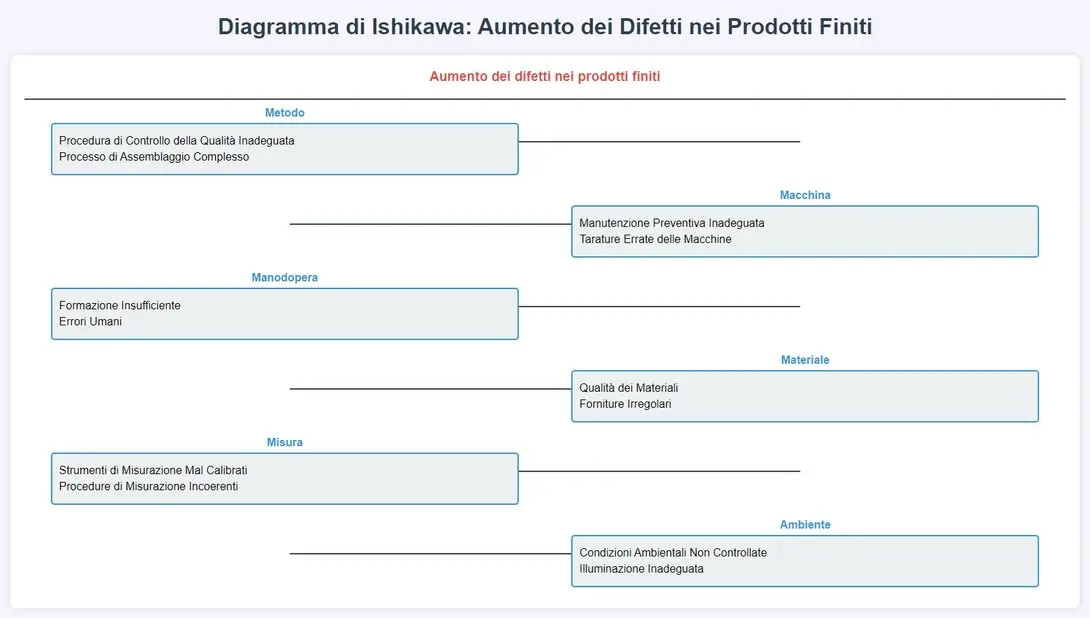
Analizzare il Diagramma
- Metodo: rivedere e semplificare le procedure di controllo della qualità e fornire istruzioni più chiare per il processo di assemblaggio.
- Macchina: implementare un programma di manutenzione preventiva regolare e assicurarsi che le macchine siano tarate correttamente.
- Manodopera: fornire formazione adeguata al personale e sviluppare strategie per ridurre gli errori umani, come pause regolari e miglioramenti nell'ergonomia del lavoro.
- Materiale: verificare la qualità delle materie prime e migliorare la gestione delle forniture per evitare ritardi e irregolarità.
- Misura: assicurarsi che tutti gli strumenti di misurazione siano calibrati correttamente e implementare procedure standardizzate per le misurazioni.
- Ambiente: controllare le condizioni ambientali nel reparto di produzione e migliorare l'illuminazione per ridurre gli errori visivi.
Pianificazione delle Azioni
- Mitigazione del Rischio di Penuria Idrica: implementare tecnologie di risparmio idrico come il riciclo dell'acqua di raffreddamento.
- Sfruttamento dell'Opportunità di Ridurre le Emissioni di CO2: investire in pannelli solari per alimentare parte del processo produttivo.
- Gestione Efficace dei Rifiuti Elettronici: stabilire un protocollo rigoroso per la raccolta e il riciclo dei rifiuti elettronici.
- Sfruttamento dell'Opportunità di Riciclare i Rifiuti Elettronici: collaborare con aziende specializzate nel recupero dei materiali preziosi dai rifiuti elettronici.
Monitoraggio e Riesame
Stabilire un piano di monitoraggio per verificare l'efficacia delle azioni intraprese, con revisioni trimestrali per aggiornare la valutazione dei rischi e delle opportunità.
3.3 Dettagliare le Cause Specifiche
Una volta identificate le categorie principali, è il momento di individuare e dettagliare le cause specifiche all'interno di ciascuna categoria. Queste cause specifiche dovrebbero rappresentare le possibili fonti di problema all'interno dell'organizzazione e possono essere identificate attraverso l'analisi dei processi, l'osservazione sul campo, il coinvolgimento del personale e l'esame dei dati disponibili.
Esempio:
- Per la categoria "Manodopera", le cause specifiche potrebbero includere la mancanza di formazione adeguata o la mancanza di competenze tecniche.
- Per la categoria "Materiale", le cause specifiche potrebbero includere la scarsa qualità delle materie prime o errori nella gestione del magazzino.
3.4 Analizzare il Diagramma
Una volta completato il diagramma, è importante analizzare le informazioni raccolte per identificare le cause più probabili del problema e pianificare le azioni correttive necessarie. Questo processo può coinvolgere il confronto delle cause identificate con dati e informazioni aggiuntive, il coinvolgimento di esperti o consulenti esterni e la valutazione dell'impatto potenziale delle azioni correttive proposte.
Esempio: Analizzando il diagramma, potremmo scoprire che la maggior parte dei difetti nei prodotti finiti è causata da errori umani nella fase di produzione. Di conseguenza, potremmo decidere di implementare un programma di formazione più completo per il personale coinvolto in queste attività.
Seguendo questi passaggi, è possibile creare un diagramma di Ishikawa completo e informativo che aiuti a identificare e affrontare le cause sottostanti di un problema specifico, facilitando la risoluzione dei problemi e il miglioramento continuo all'interno dell'organizzazione.
4. Utilizzi dei Diagrammi di Ishikawa
- Risoluzione dei Problemi: identificare e analizzare le cause di un problema.
- Gestione della Qualità: migliorare i processi produttivi e la qualità dei prodotti.
- Pianificazione dei Progetti: identificare potenziali rischi e problemi prima che si verifichino.
- Formazione e Coinvolgimento del Personale: favorire la collaborazione e il brainstorming tra i membri del team.
5. Esempio Pratico di Diagramma di Ishikawa
5.1 Contesto Aziendale
Un'azienda di produzione di componenti elettronici riscontra un aumento dei difetti nei prodotti finiti. Per identificare le cause del problema, l'azienda decide di utilizzare un diagramma di Ishikawa.
5.2 Fasi del Diagramma
1. Identificazione degli Aspetti Ambientali
- Consumo di acqua: monitoraggio del consumo di acqua nei processi di produzione.
- Emissioni di CO2: misurazione delle emissioni di CO2 derivanti dalle attività produttive.
- Produzione di rifiuti elettronici: quantificazione dei rifiuti elettronici generati.
2. Valutazione degli Impatti Ambientali
- Significatività di ciascun aspetto: valutazione della gravità degli impatti ambientali legati al consumo di acqua, emissioni di CO2 e produzione di rifiuti elettronici.
3. Conformità Legale e Altri Requisiti
- Verifica della conformità normativa: controllo del rispetto delle normative ambientali e degli standard di settore.
4. Raccolta di Dati e Informazioni
- Dati su consumo di acqua: raccolta di dati sul consumo di acqua nei processi produttivi.
- Dati su emissioni: raccolta di dati sulle emissioni di CO2.
- Gestione dei rifiuti: raccolta di dati sulla produzione e gestione dei rifiuti elettronici.
5.3 Come Creare un Diagramma di Ishikawa
1. Definire il Problema
Identificare chiaramente il problema da analizzare. In questo caso: "Aumento dei difetti nei prodotti finiti".
2. Identificare le Categorie Principali (6M)
- Metodo: Procedura di Controllo della Qualità Inadeguata, Processo di Assemblaggio Complesso.
- Macchina: Manutenzione Preventiva Inadeguata, Tarature Errate delle Macchine.
- Manodopera: Formazione Insufficiente, Errori Umani.
- Materiale: Qualità dei Materiali, Forniture Irregolari.
- Misura: Strumenti di Misurazione Mal Calibrati, Procedure di Misurazione Incoerenti.
- Ambiente: Condizioni Ambientali Non Controllate, Illuminazione Inadeguata.
3. Elencare le Cause
- Sotto ciascuna categoria, elencare tutte le potenziali cause del problema.
4. Disegnare il Diagramma
- Disegnare la "testa" del pesce con il problema principale.
- Disegnare la "spina dorsale" orizzontale.
- Aggiungere le "lische principali" (categorie) che si diramano dalla spina dorsale.
- Aggiungere le "lische secondarie" (cause) sotto ciascuna categoria.

6. Conclusione
I diagrammi di Ishikawa sono strumenti efficaci per la risoluzione dei problemi e il miglioramento continuo della qualità. Offrono un approccio strutturato e visivo per analizzare le cause di un problema, facilitando la comprensione e la comunicazione all'interno dei team di lavoro.
7. Domande Frequenti sul diagramma di Ishikawa
Vedi le domande frequenti sul diagramma di Ishikawa e le nostre risposte.